EnLighten your luminaire with new patented DOWSILTM EI-2888 Primerless Silicone encapsulant. This innovative solution will help you in addressing the processing and cost challenges by providing good primerless adhesion, inhibition resistance and superb optical clarity.
Whether you are using existing organic or silicone solutions with primer, we encourage you to join our talk and discover how DOWSILTM EI-2888 will help you to improve your process and luminaire performance and reliability.
DOWSILTM EI-2888 Primerless Silicone encapsulant has been specifically developed to protect LED luminaires used in harsh environment such as explosion proof and high ingress protection (IPxx) rated luminaires. Thanks to its unique rheological properties it can be used for lighting fixtures of different shape and form.
Register now here to learn more and request a sample of DOWSILTM EI-2888.
February 21, 2019 at 9:00 AM EST / 8:00 AM CST / 6:00 AM PST / 3:00 PM CET
Presented by:
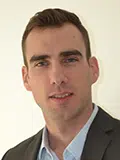
Dow Silicones Belgium SPRL
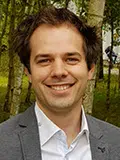
Technical Service & Development Specialist
Dow Silicones Belgium SPRL
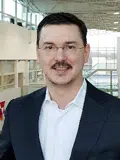
Strategic Marketing Manager
Dow Silicones Belgium SPRL
Moderator:
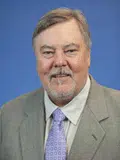
Editor-in-Chief
LEDs Magazine
About the new product:
DOWSIL™ EI-2888 Primerless Silicone Encapsulant
Optically clear, 2-part 1:1 mix ratio, low viscosity, self priming silicone encapsulant
DOWSILTM EI-2888 Primerless Encapsulant is supplied as two-part liquid component. When liquid components are thoroughly mixed either by weight or volume, the mixture cures at room temperature or with mild heat to a flexible elastomer, which is well suited for the protection of rigid and flexible circuit boards for indoor or outdoor LED Lighting, explosion proof and high ingress protection rated luminaire as well as outdoor displays.
Dow silicone encapsulants cure without exotherm at a constant rate regardless of sectional thickness or degree of confinement. This encapsulant contains its own source of moisture, so cure progresses evenly throughout the material and deep-section or confined space cures are possible.
Self priming encapsulant develop reliable adhesion to a wide range of substrates at room temperature or with mild heat, without the need of primer. Only good cleaning may be needed.
Unlike other silicone chemistries, this product is unsensitive to phenomena like Platinum catalyst inhibition when exposed to contaminant, or material reversion when exposed to high temperature in a confined environment.
Dow silicone elastomers require no post cure and can be placed in service immediately following the completion of the cure schedule.
Dow silicone elastomers retain their original physical and electrical properties over a broad range of operating conditions which enhance the reliability of and service life of devices.
Features & Benefits
- Room temperature cure with optional heat acceleration
- Low viscosity – ease of processing
- Self priming – no primer needed
- 100% silicone (PDMS)
- UL 94 recognized
Applications
DOWSIL™ EI-2888 Primerless Silicone Encapsulant is particularly suitable for encapsulating rigid and flexible circuit boards for indoor and outdoor LED Lighting, explosion proof and high ingress protection rated luminaire as well as outdoor displays applications.
Application Methods
- Automated static or dynamic metered mixing
- Manual mixing
- Flow, pour, or needle dispense
Processing/Curing
Thoroughly mixed Dow silicone encapsulant may be poured/dispensed directly into the container in which it is to be cured. Care should be taken to minimize air entrapment. When practical, pouring/dispensing should be done under vacuum, particularly if the component being potted or encapsulated has many small voids. If this technique cannot be used, the unit should be evacuated after the silicone encapsulant has been poured/dispensed. Dow silicone encapsulants may be either room temperature (25°C/77°F) or heat cured (max 60°C/140°F). Room temperature cure encapsulants may also be heat accelerated for faster cure. Ideal cure conditions are given in the product selection table.
Time to cure is dependent on several variables including the method of application, film thickness, temperature and humidity. Gel time in the data table gives an indication of typical times to form a gel. Cure time for full cure are indications of time needed to develop full physical properties such as durometer, tensile strength or adhesion. These times, including full cure time, can be significantly improved by introducing mild heat of 60°C/140°F or less.
Adhesion does not need the full cure schedule to develop, material can therefore be put in service before finishing the full cure schedule in majority of the cases. Optimum cure schedules should be determined in each new application.
Pot Life and Cure Rate
Cure reaction begins with the mixing process. Initially, cure is evidenced by a gradual increase in viscosity, followed by gelation and conversion to a solid elastomer. Pot life is defined as the time required for viscosity to double after DOWSIL™ EI-2888 Primerless Silicone Encapsulant Part A and DOWSIL™ EI-2888 Primerless Silicone Encapsulant Part B (base and curing agent) are mixed and is highly temperature and application dependent. Please refer to the data table. Gel time in the data table gives an indication of typical times to form a non-flowing gel. Cure time for full cure are indications of time needed to develop full physical properties such as durometer, tensile strength or adhesion
Adhesion
Dow self priming encapsulants are formulated to provide adhesion to most common substrates and materials. It is recommended that the encapsulant be applied to clean and dry substrates prior to application. Due to the vast variety of substrates used, general statements on adhesion and bond strength are impossible. Appropriate adhesion testing should be performed to insure the adhesion of the encapsulant is adequate for the end use.
As adhesion evolve with time during cure, adhesion will increase until full cure at room temperature. On certain difficult, low-surface energy surfaces, adhesion may be improved by priming or by special Dow self priming encapsulants are formulated to provide adhesion to most common substrates and materials. It is recommended that the encapsulant be applied to clean and dry substrates prior to application. Due to the vast variety of substrates used, general statements on adhesion and bond strength are impossible. Appropriate adhesion testing should be performed to insure the adhesion of the encapsulant is adequate for the end use.